Making Their Mark: Josh Haywood
By Anna Tutty
July 1, 2020
Long before lockdown, WATG and Wimberly Interiors’ global network of designers, makers and creators have looked beyond their every day to inspire ideas and innovations. In this new series, Making Their Mark, we shine a spotlight on our team members and creative associates, and the passion projects they pursue outside of 9–5 – not only for their personal mental health, well-being and growth, but for the benefit of their clients, projects and colleagues. Fostering a spirit of creativity, innovation, individualism and imagination among our ohana (family) has been central to our firm since its founding seventy-five years ago, and we are proud to support one another not only at work, but externally as well.
In the first interview of the series, we speak with Josh Haywood – an Architect at WATG London who specialises in computational design. In addition to his impressive at-work portfolio which spans the Middle East, Europe and Asia, Josh is an accomplished artist whose 3D printed structures have graced the likes of Burning Man, the Versace autumn/winter runway in Milan and, soon, one of London’s busiest train stations.
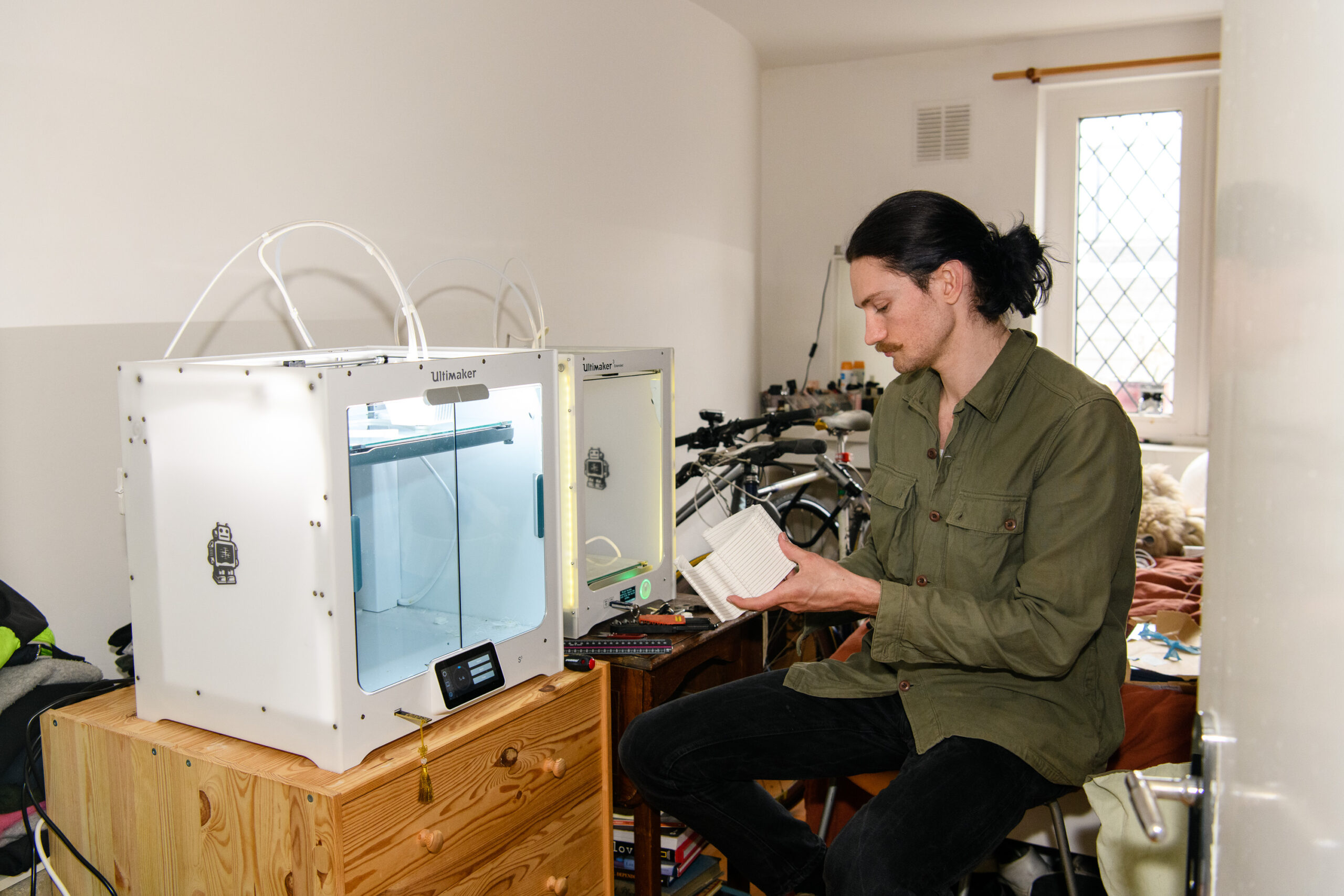
At the beginning of London’s lockdown, Josh teamed up with Helpful Engineering UK to assist in the creation of PPE for London hospitals
Josh, tell us a little bit about your career and what a ‘normal’ day looks like for you.
I have been with WATG for two-and-a-half years now, and in that time I’ve been able to work with three different studios/senior leaders across a range of briefs and scales. The variety and profile of projects within the practice have meant there’s never been a dull moment, and I’m always learning from the new challenges on offer.
On the road to working at WATG, I was with Foster and Partners for two years, and ran my own business for a further two, specialising in computational design and digitally led fabrication. When involved in project work I try to elevate the use of computational workflows – primarily with Grasshopper for Rhino – to enhance the output of the studio. There is a growing interest within the London office for parametric design, and with the help of some very interesting recent competition briefs the benefits of digitally led design are coming to the forefront.
A typical day in the office before lockdown involved eight hours of project work, a hurried squash game through lunch, and a few impromptu desk-side Grasshopper tutorials amongst the team. Now working from home, a few of those luxuries have changed but there is still a spirit of discovery in the team. We share our work and ideas frequently on Zoom, and will soon be holding short online presentations and tutorials for the rest of the team.
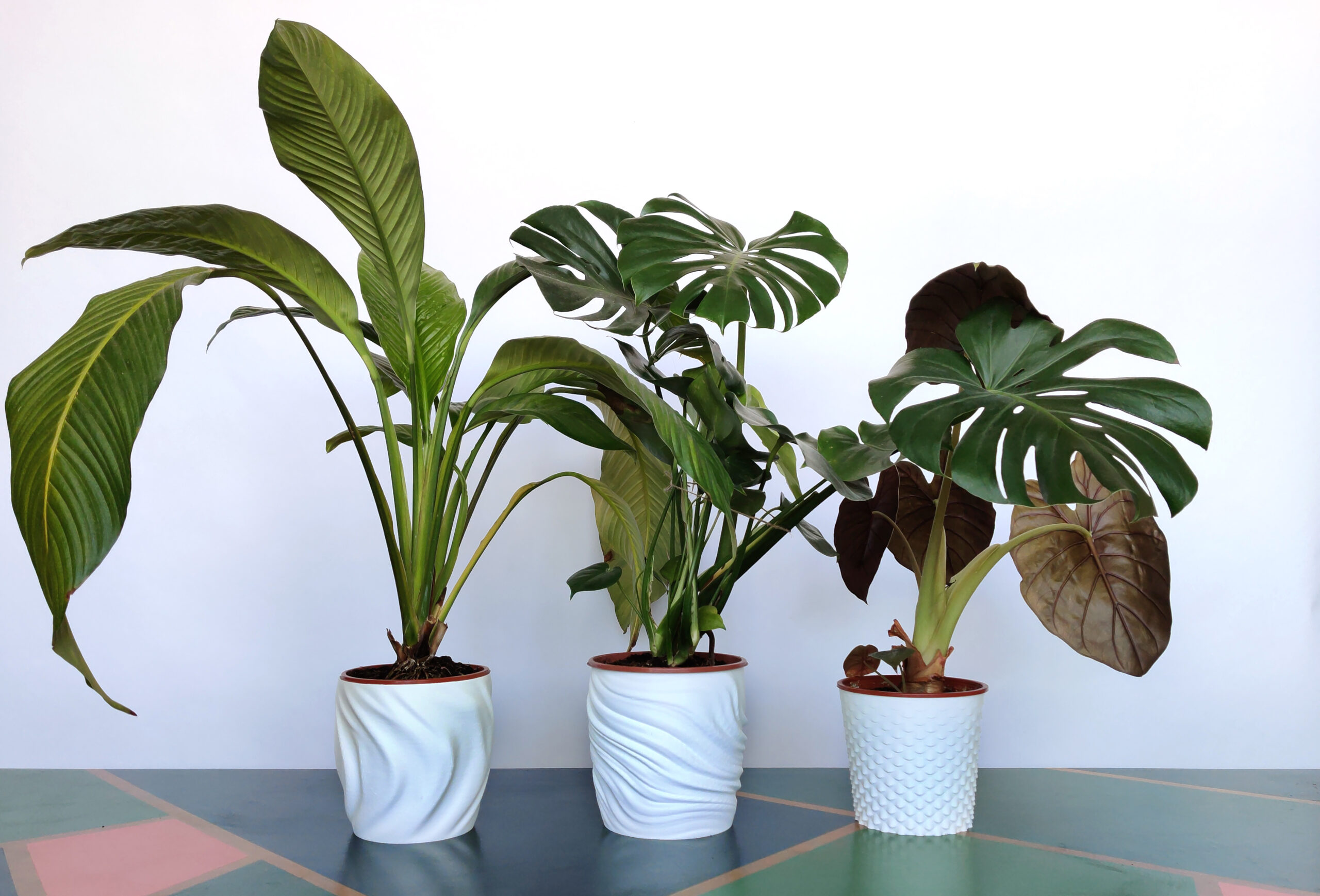
An experiment in generating complex geometry through algorithmic design results in 3D printed planters
In isolation we’ve been forced to find new outlets for entertainment and inspiration. Talk us through your side project(s). What is it and how did it begin?
As the lockdown dawned upon London I searched for ways to volunteer and help the NHS during the growing crisis. I’d seen designers and makers in Spain and Italy who were ahead in the pandemic timeline try to address the PPE supply problems by 3D printing visors. Together with my flat mate we sought out a group who were producing and distributing PPE, and volunteered to help.
In the beginning, we were helping by cycling between fabricators and hospitals, transporting their printed and laser cut PPE items, but we wanted to contribute further by adding to the network of 3D printers producing equipment. I discussed the idea of utilising WATG London’s 3D printers as part of this drive with our Managing Director, Martin Pease, who was very supportive of the idea. We quickly moved to relocate the printers to my apartment for streamlined production. Through a combined WATG team effort we put in an extra 500 visors to the PPE network before regulations came in stifling the maker movement of PPE production.
After I could no longer make an effective contribution to the PPE shortage, I looked for other ways to turn the 3D printers to good use – there was an array of plants around my home longing to be housed in new pots so I turned my attention to printing these in a host of different sizes and designs. It has been a good exercise in generating complex geometry through algorithmic design, and learning how to optimise the printing code for fast, successful production. Upon our return to the office, this development will be able to be feed into live project work at WATG, where we frequently produce 3D printed models during the design process.
Another project of interest that is currently active is a bench I am producing for London Victoria train station, commissioned by Network Rail. This bench will also be 3D printed, but by industrial robotic arms to enable the large print volume required for making objects of scale. The bench is designed with the circular economy of materials in mind; it is produced from recycled material, and at the end of its life cycle it can be ground into pellets for use in printing future bench design iterations. This makes 3D printing a sustainable alternative to traditional station seating manufacturing methods that typically use steel, timber, or concrete, that are much harder to recycle and more wasteful in their production. It is hoped that the Victoria Station project will set a precedent for the future of urban furniture.
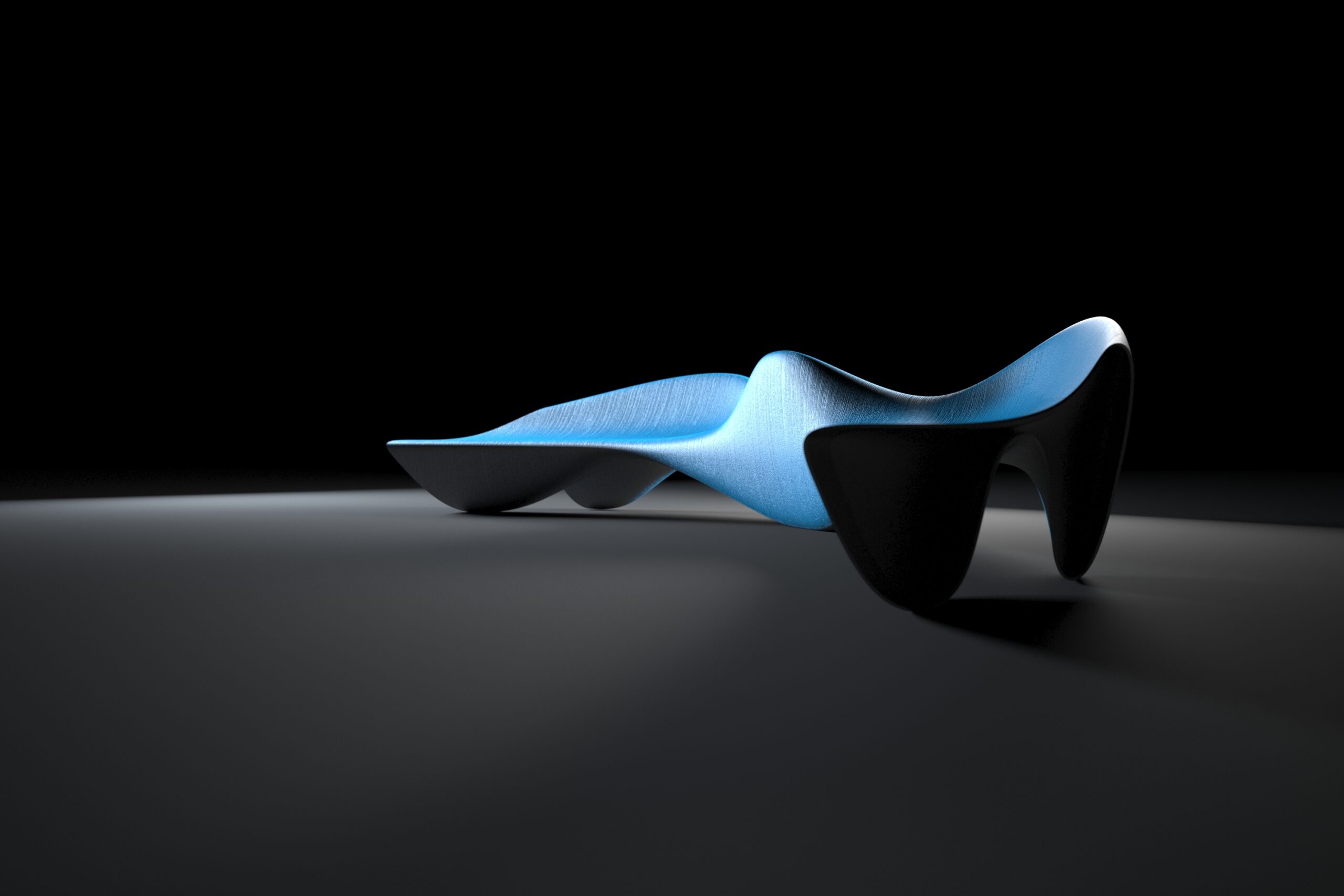
At the end of its life cycle, ‘Beluga’ can be ground into pellets for future bench design iterations
Have you found this new creative process to be cathartic or challenging? Has anything about it surprised you?
The best surprise has been seeing how in these times of uncertainty, anxiety, and change, people come together to help each other and find ways to better the situation for everyone. I’ve only played a tiny part but it is rewarding to be part of the larger family of volunteers, and to have the generous support of WATG in allowing its machines to be repurposed while the London office is closed.
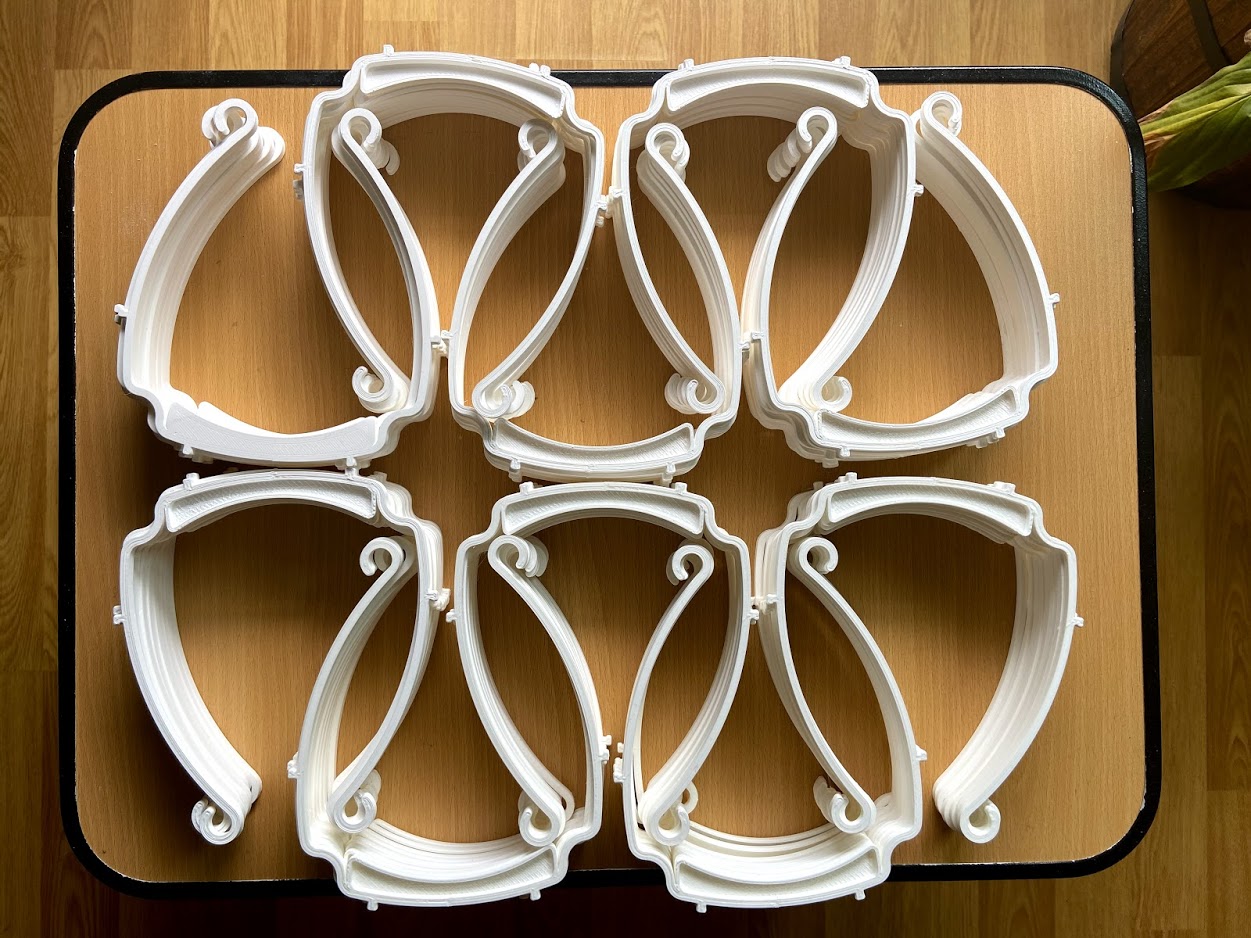
WATG’s 3D printers were relocated to Josh’s home to assist in the procurement of PPE for the NHS
How has being creative outside of work positively impacted your outcomes at work?
Keeping creative projects outside of the studio active is a great way keep design work fresh and invigorating, and to put technical skills learned at work to new challenges. A lot of studio work doesn’t require the application of a computational design methodology, and through these side-gigs I keep my knowledge up-to-speed so when the right projects arise in the studio I’m best equipped to contribute to them.
When producing PPE for the NHS I teamed up with a group called Helpful Engineering UK. Through this network I met many like-minded individuals within the building and construction industry. Being part of a big network of peers helped me grapple with the challenges and frustrations of being part of a huge team, and in returning to the WATG team feel humbled, and enthused to be part of something bigger than oneself.
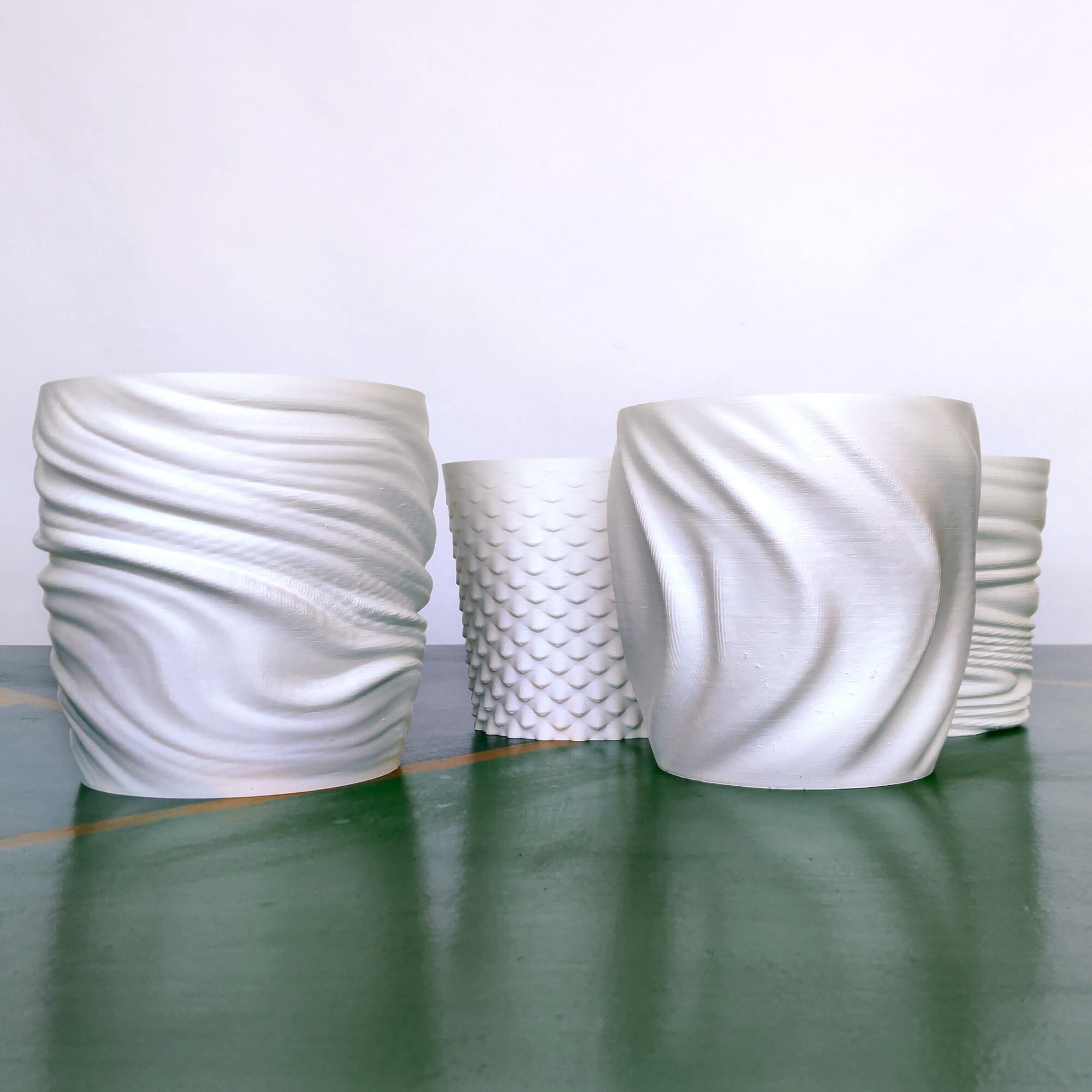
3D printed planters aim to optimise fast, successful production of future WATG models
Tell us a little bit about a maker or creator who has inspired you, and why.
I love to follow the work of designers, artists and architects doing great things with technology; Marc Fornes, Ball-Nogues Studio, and Wolfgang Buttress to name a few. Whenever I see an installation or structure and can’t get my head around how it was fabricated/manufactured, I’m compelled to find out.
You can follow Josh on Instagram here, and Hylemo here. You can also visit the Hylemo website for more information.
Latest Insights
Perspectives, trends, news.
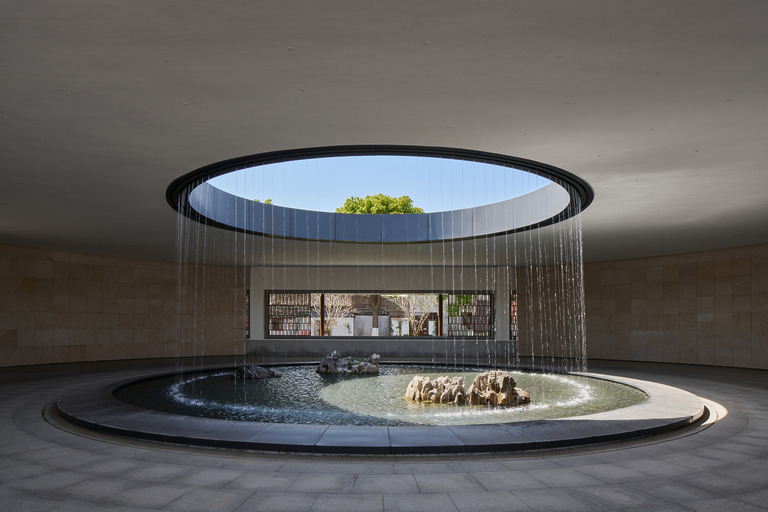
- Strategy & Research |
- Design Thinking & Innovation
Designing the Arrival Experience
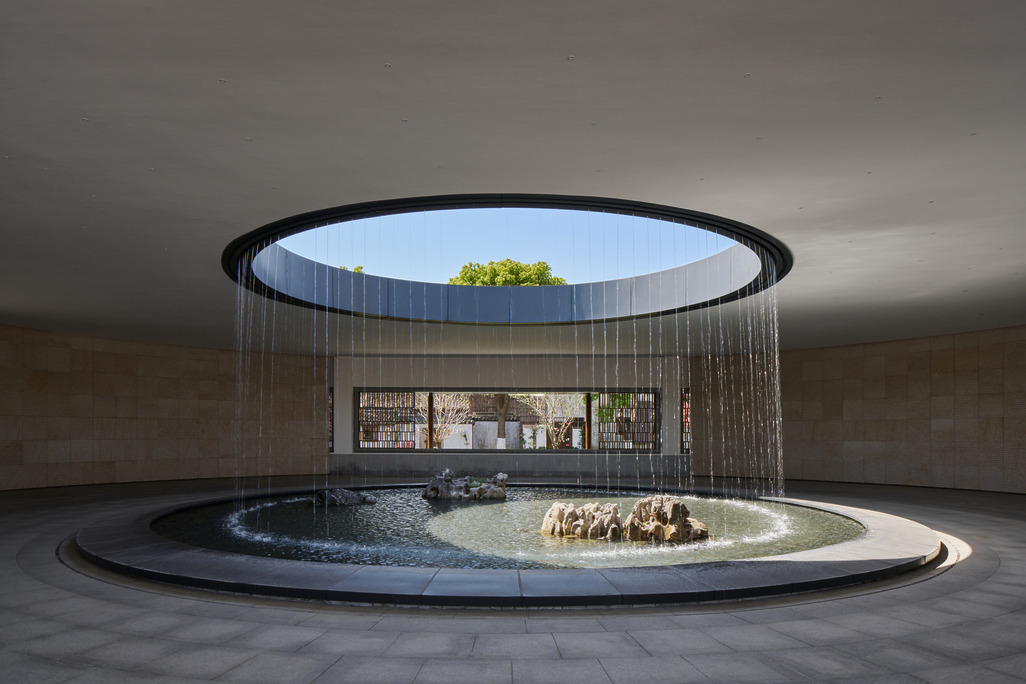
- Strategy & Research |
- Design Thinking & Innovation
Designing the Arrival Experience
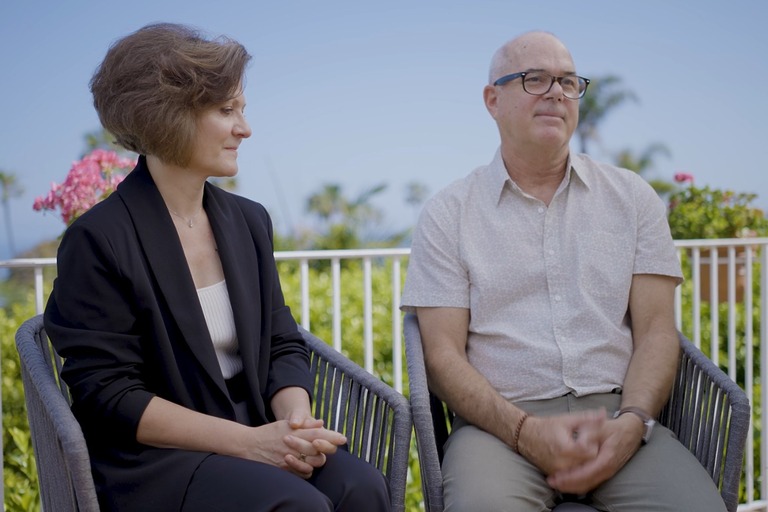
- Employee Feature |
- Inside WATG
Mentorship, Community, and Creativity: WATG’s Blueprint for the Next 80 Years
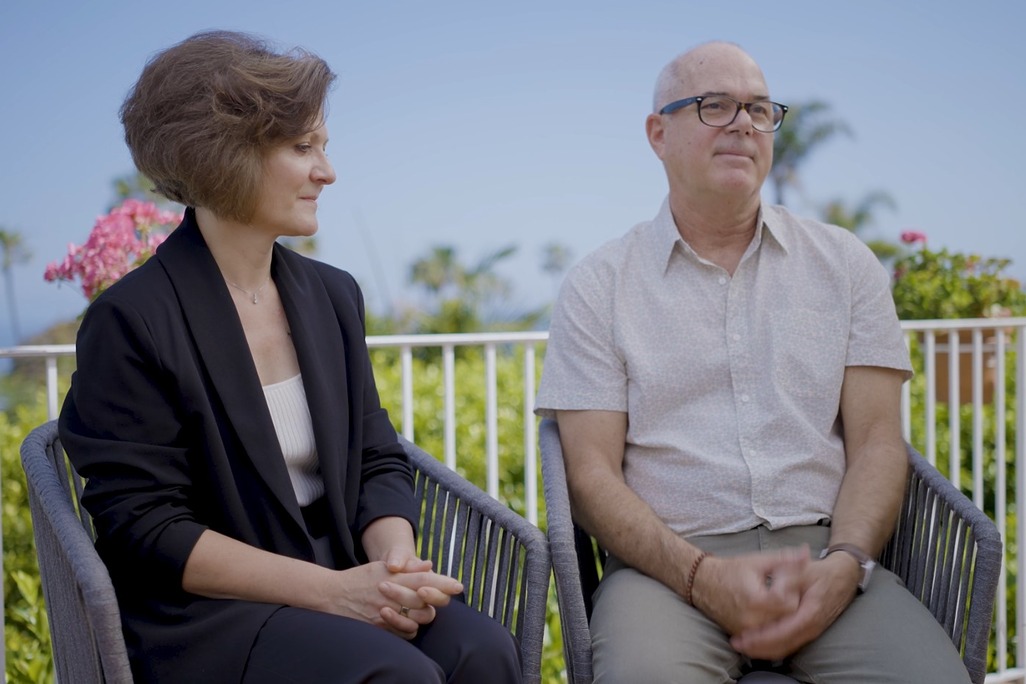
- Employee Feature |
- Inside WATG
Mentorship, Community, and Creativity: WATG’s Blueprint for the Next 80 Years
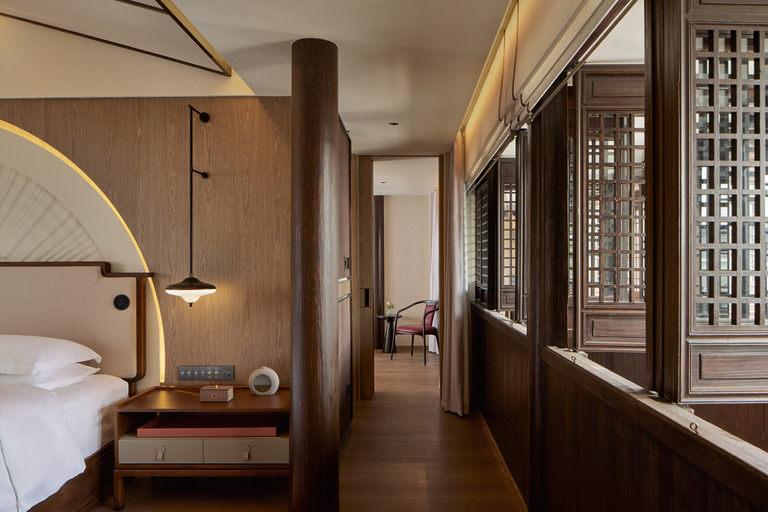
- Strategy & Research |
- Design Thinking & Innovation
Hotel Wuxi MGallery Collection: Part of a Story
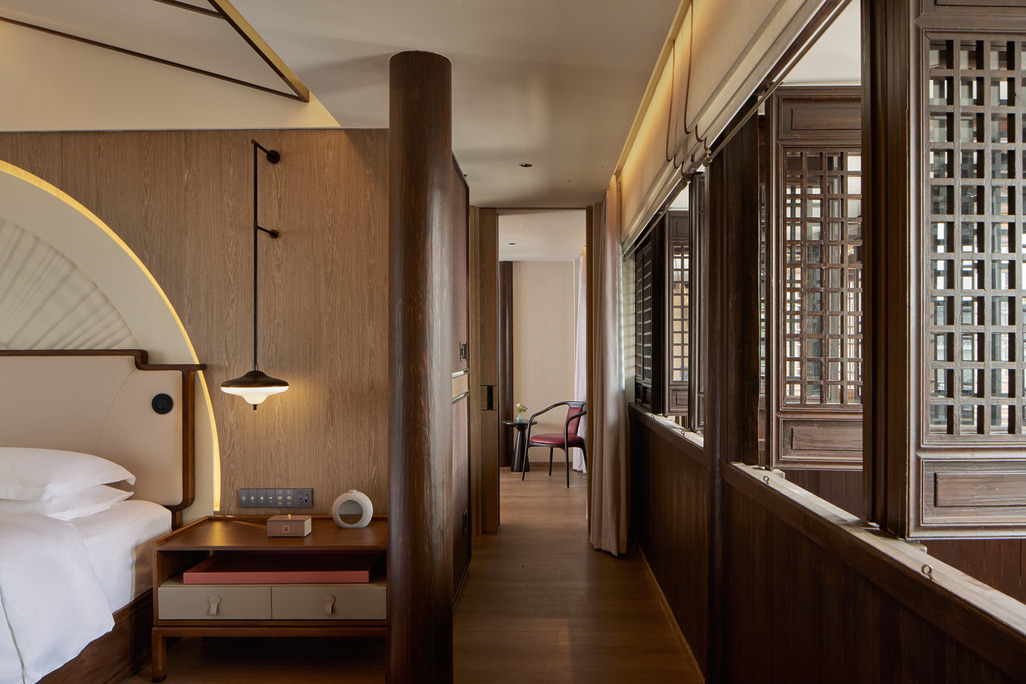
- Strategy & Research |
- Design Thinking & Innovation
Hotel Wuxi MGallery Collection: Part of a Story
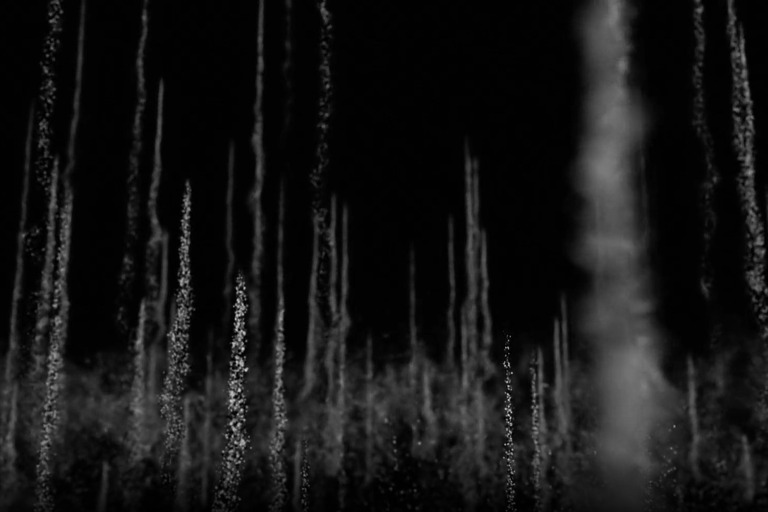
- News
Behind The Scenes: ‘We Create Moments’
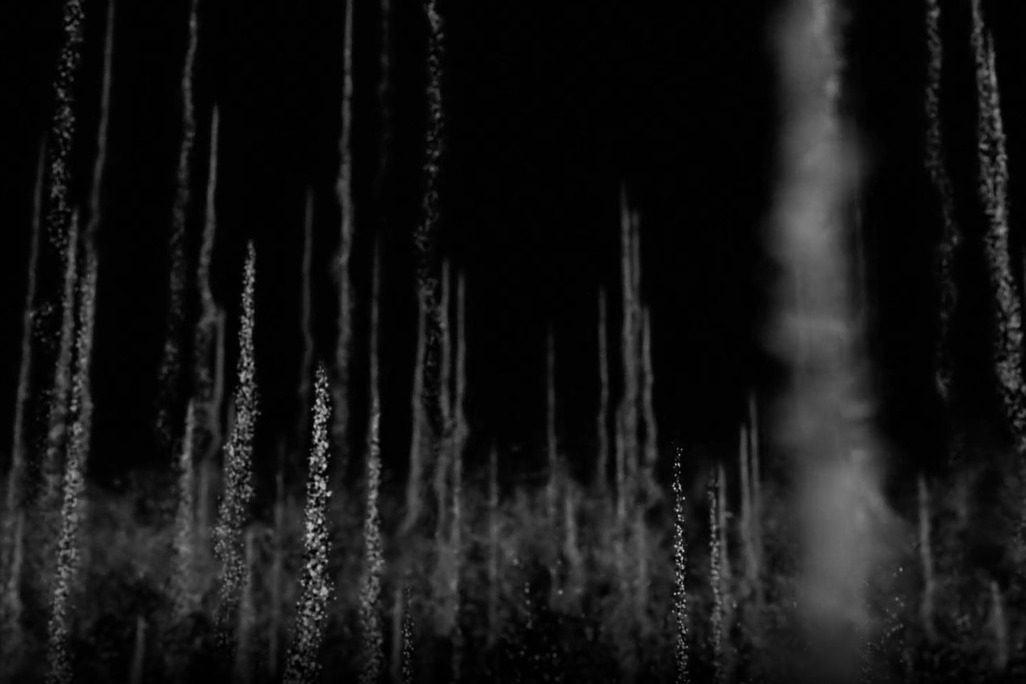
- News