Craftsmanship made possible through robot construction
By WATG
April 28, 2020
During Daniel Caven’s first week at WATG’s former Chicago office, he spied a competition call for entries by Tennessee’s Branch Technology to design a 3D-printed house. The opportunity to engage his unshackled imagination proved too tantalizing to ignore and he spent the next eight days crafting a design.
“This project says ‘here’s the future of construction’.”
He’d completed some 3D printing design before for a project in Dubai. But this was different. Branch promised an innovative technology called cellular fabrication that enabled him to design a home with a flowing interior space creating privacy, yet also opened to the outside. “It made conceptual design become real,” he says. “It’s truly free-form so we can bring all these really luxurious curves and undercuts and all these beautiful spaces to life with this technology.”
The house, appropriately named Curve Appeal, caught the eye of Branch co-founder R. Platt Boyd and was chosen over more than 1,300 other entries from 97 countries. “He definitely was pushing the envelope so hard and really highlighting what’s possible,” Boyd says. “This project says ‘here’s the future of construction’.”
In the years since, as Curve Appeal moved from design to printing, Caven has worked with Branch to uncover the promise of the firm’s patented technology. Unlike other 3D printing techniques, which layer concrete atop concrete, for example, Branch’s pioneering process creates a lightweight carbon fiber reinforced scaffolding printed by a robot that turns a designer’s concept into reality. Virtually any form can be created. There’s little compromise when the project moves from the design phase to the construction phase. The material is three to four times stronger than traditional wood construction.
“Working with their system brings on so many new and different strategies and brings up new ideas,” he says. “It’s like seeing the world for the first time through the use of this technology. It’s freeform so you’re able to do crazy ornate and beautiful curvilinear forms.”
“With this technology, we can be both resilient for the planet and creative for our clients.”
Now, Caven and the designers at WATG are turning their attention to the possibilities that go beyond the cutting-edge design enabled by the technology. Bryan Algeo, who has shepherded projects that fit seamlessly into the cultural, environmental, and commercial desires of clients in 20 countries, says this flexible 3D printing will transform residential and resort design over the coming decade. “With this technology, we can be both resilient for the planet and creative for our clients. It’s a win for the environment and a win for our design process.”
Algeo and Caven see Branch’s technology coupled with WATG’s worldwide design experience giving rise to a new way of building that will land a lighter footprint on sensitive landscapes. In remote locales, Algeo notes, skilled labor often has to be imported and housed on a construction site, which is costly, time-consuming, and disruptive to the environment. With 3D printing, pieces could be built off-site and shipped to solve those problems. The structures could be organic, designed to fit with the topography, not just imposed on the site. The process is greener, with literally no construction waste. “We often find ourselves in remote, pristine locations,” Algeo says. “Many times there aren’t skilled workers and contractors and the materials required to produce these structures. It takes a lot of people to build these places. And that can end up permanently damaging the land.” Having a robot build the pieces of a structure makes custom-design on a mass scale cost-effective, they note. “It’s a game-changer for architects and designers,” Caven adds. Hotel rooms, for instance, could be customized with prefabricated walls, giving each one that individual touch.
Algeo imagines habitats for resort clients that can be ferried from place to place as demand ebbs and flows, perhaps from a mountaintop in summer to the desert in winter. “They can be fairly lightweight, move with the seasons, and increase the occupancy of a destination,” he adds.
There’s precedent. Branch has used the technology to create the world’s largest free‐form, 3D‐printed hanging garden installation, “Nature Clouds,” at Chicago’s Field Museum of Natural History, an open pavilion for a Nashville community lawn that spans 42 feet, and the prototype of a Mars habitat for NASA.
When people start looking for places to go as the travel faucet slowly reopens, they likely will be looking for more remote destinations, perhaps aiming to connect with nature in the mountains of California, the shoreline of Mexico, or the rainforest of Costa Rica. Designing and building with 3D printing could pave the way to develop appealing new ways for resorts to build the kind of remote, intimate lodging travelers will seek without damaging their natural appeal. “The essence of this is letting people experience these places in their natural state,” Algeo says.
“We’re seeing the beginning stages of this transition to usher this technology into the world.”
For WATG, Caven’s work with Branch Technology over the past four years puts the firm on the leading edge of transforming construction techniques largely unchanged for centuries. Branch’s Boyd likens 3D printing technology today to the eve of the microchip age decades ago. “It’s really exciting,” he says. “We’re seeing the beginning stages of this transition to usher this technology into the world.”
For Curve Appeal, Caven and the Branch teamed to work through the structural engineering challenges, keeping the design intact. The house is a sort of puzzle of oddly-shaped Lego pieces, 130 parts in all ranging anywhere from eight to 27 feet long that took from hours to days to print.
It’s an example of the craftsmanship made possible by merging a designer’s unfettered imagination with the endless possibilities of robot construction. Man and machine building what only a few years ago seemed impossible. The Curve Appeal house that will be completed later this year is an uncompromising result of WATG’s design team’s vision.
“It’s such an amazing thing,” Caven says. “We’re coming to a new phase in architecture.”
Latest Insights
Perspectives, trends, news.
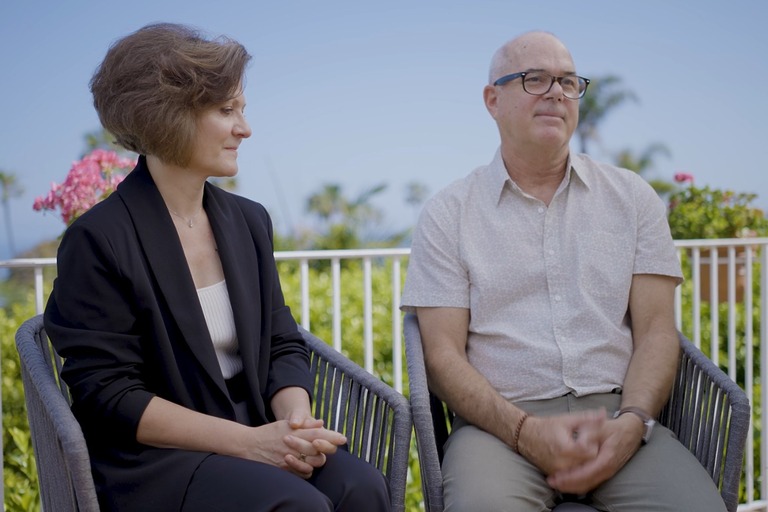
- Employee Feature |
- Inside WATG
Mentorship, Community, and Creativity: WATG’s Blueprint for the Next 80 Years
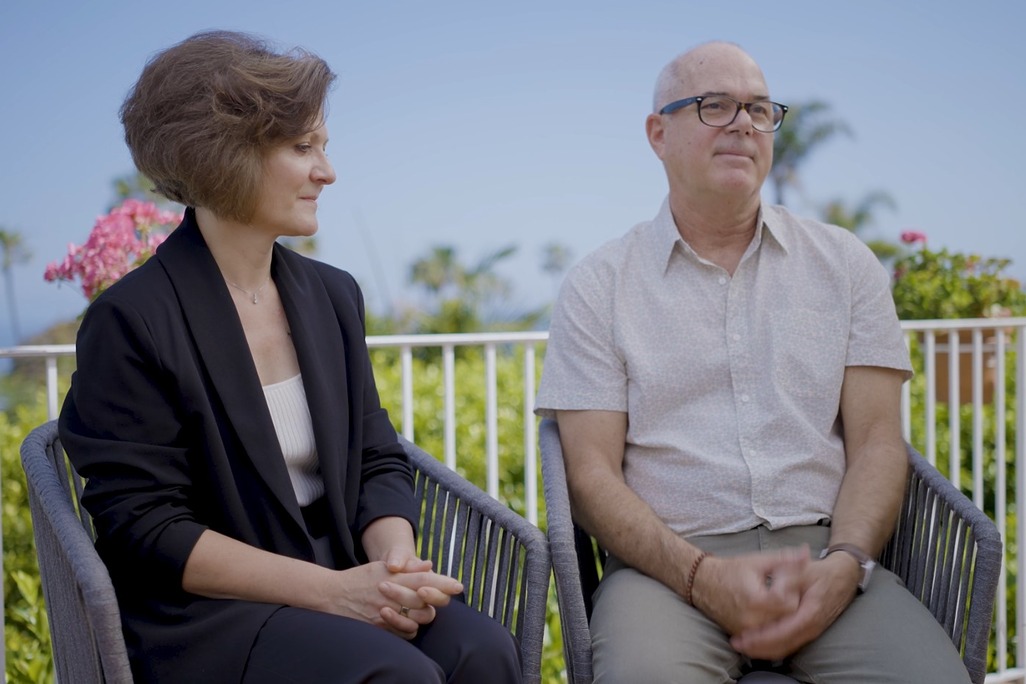
- Employee Feature |
- Inside WATG
Mentorship, Community, and Creativity: WATG’s Blueprint for the Next 80 Years
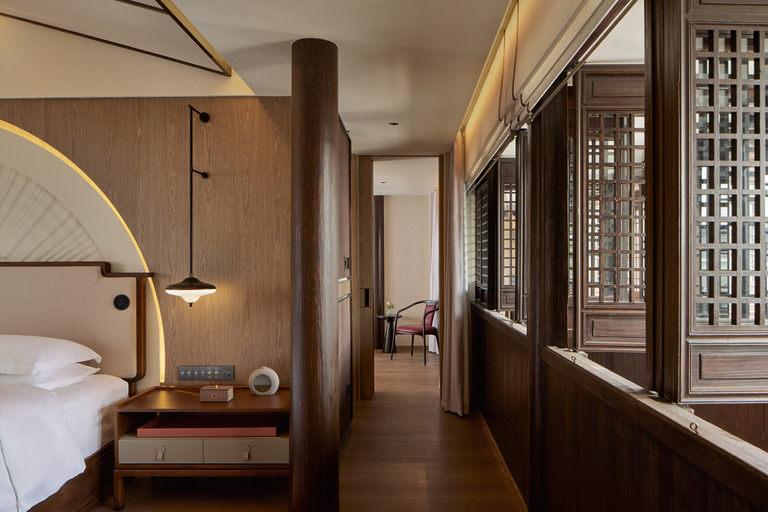
- Strategy & Research |
- Design Thinking & Innovation
Hotel Wuxi MGallery Collection: Part of a Story
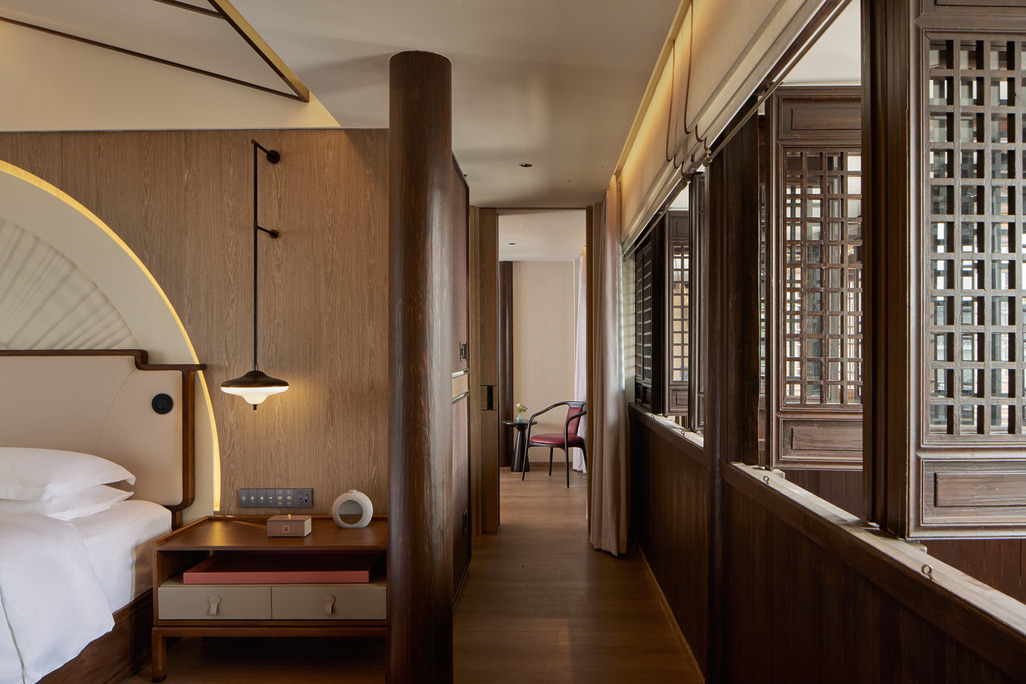
- Strategy & Research |
- Design Thinking & Innovation
Hotel Wuxi MGallery Collection: Part of a Story
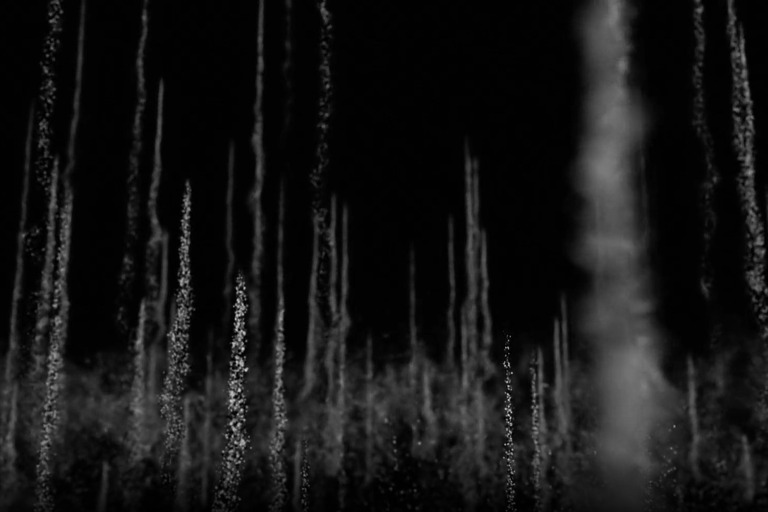
- News
Behind The Scenes: ‘We Create Moments’
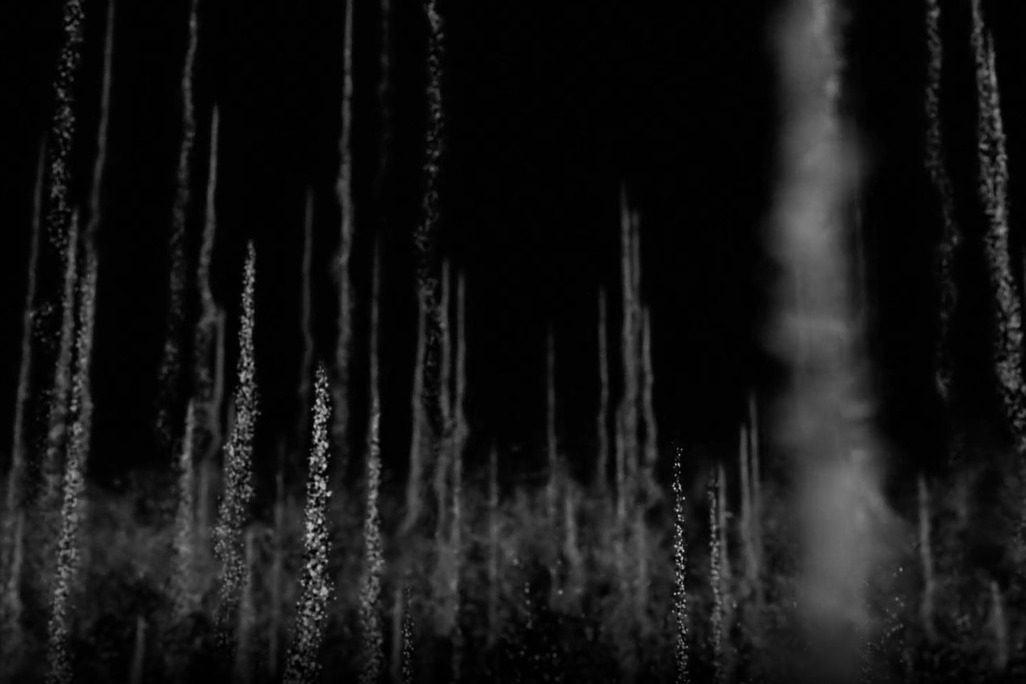
- News
Behind The Scenes: ‘We Create Moments’
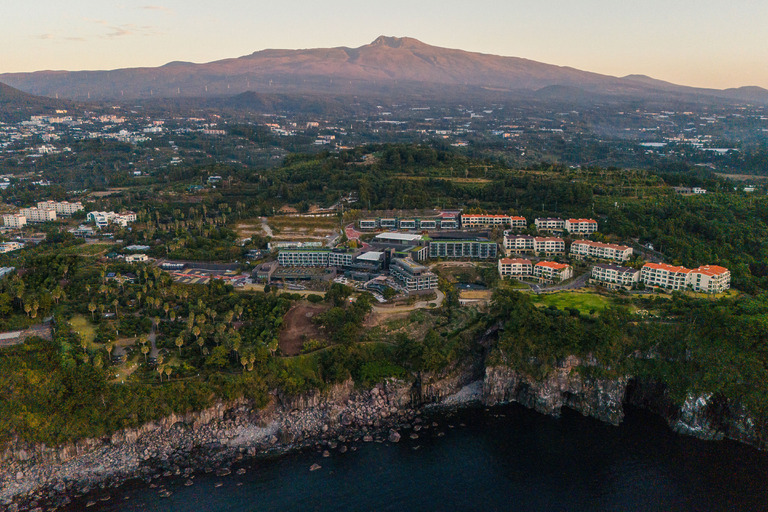
- News
Hotel Room 404: The Mystery of the Missing Floor
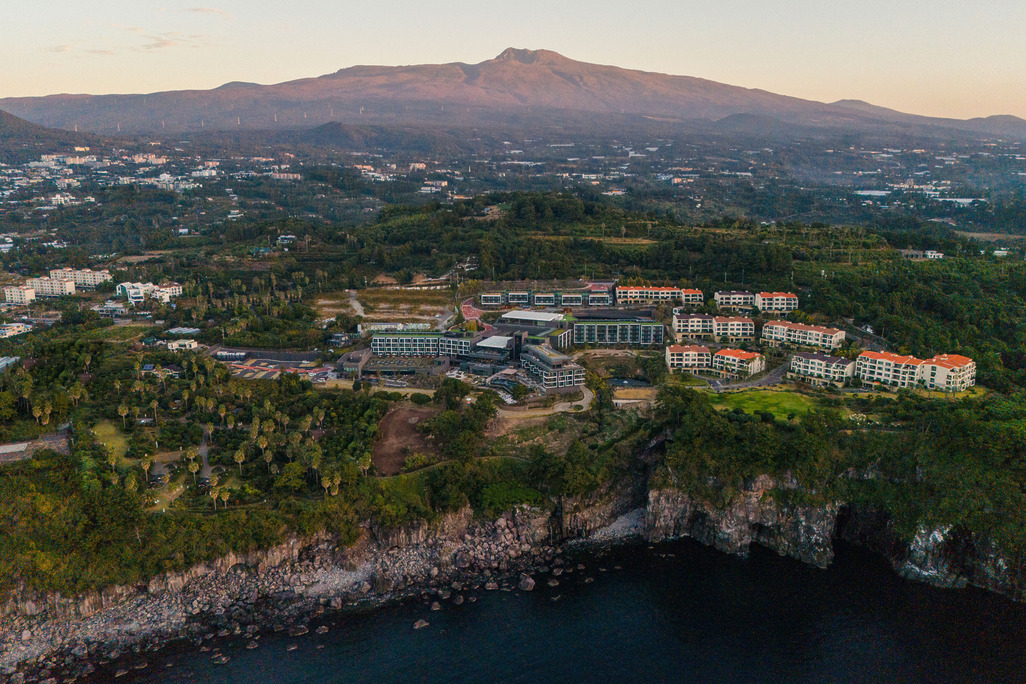
- News